Active Projects
Autonomous Exploration and Extraction of Deep Mineral Deposits
Acronym PERSEPHONE
The Aim
The continuous effort and increased demand of the raw materials are directing the mining companies to excavate minerals at greater depths. This trend is challenging the current mining operations and the existing traditional technologies towards the objective to retain profitability, while achieving the latest Green Deal environmental vision and securing human workers safety. A key enabler, to address these challenges and to foster a sustainable development of the mining industry, is the development and deployment of innovative technologies for resource efficient extraction of the EU’s raw materials, as well as near mine exploration of critical raw materials in currently non-extracted ore bodies in existing or abandoned ones.
PERSEPHONE is aiming to address these challenges by developing of the pioneering technologies for pushing the limits of EU mining industry and embodiment of autonomous and integrated near mine exploration capability to access deep deposits of critical raw materials through hard-to-reach deep and abandoned mines. The overall concept and vision of PERSEPHONE will be achieved by reducing the size of mining machines currently adapted to the human scale and embedding autonomy for risk-aware navigation and full digitalization of the extraction process by digital twin creation and key enabling technologies validation at TRL 5. Additionally, PERSEPHONE is introducing completely novel approaches in online near mine exploration core analysis and overall integration of related data analytics to the mine expansion. Thus, PERSEPHONE allows to foster green transition by reducing the cost and waste generated from deep-mining operations and foster the vision of zero human presence in highly hazardous areas. These will allow to achieve PERSEPHONE’s overall goal to digitalize and automate extraction value chain by creation of new concepts of energy-efficient autonomous drilling machines with advanced perception capabilities for navigation, face drilling, and core extraction, which will enable data-driven digital twin creation and geological modelling for further enhanced decision support and optimal extraction planning.
- Type of Action HORIZON-RIA
- HORIZON-CL4-2023-RESILIENCE-01-02
- 1/1/2024-31/12/2027
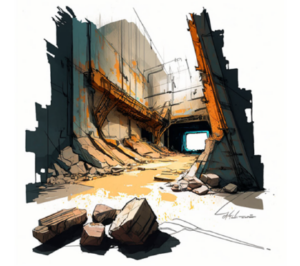
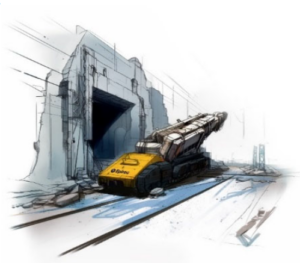